
How can the best gear shaper cutter reduce downtime?
Table of Contents
ToggleHow can the best gear shaper cutter reduce downtime? Complete Guide
How can the best gear shaper cutter reduce downtime? This remains a key concern in automotive, aerospace, and related industries. Precision and accuracy in gear manufacturing directly impact machinery efficiency and durability, emphasizing the need for tools that enhance performance while reducing delays.
A gear shaper cutter is an important tool across manufacturing industries since it is responsible for the accuracy of gears. Choosing the right tool cutter reduces downtime since it gives the best performance and minimal chance of error. A smaller number of defects on selected places is obtained by precision cutting, which reduces the amount of rework time required and increases productivity.
Understanding Gear Shaper Cutters
Gear shaper cutters are specialized tools used in the manufacturing of gears through a shaping process. They utilize a reciprocating cutting motion to gradually form gear teeth with high precision. The cutter is mounted on a machine and engages with the workpiece to remove material step by step until the desired gear profile is achieved.
There are several types of gear shaper cutters, including:
- Disc-type cutters are suitable for general gear-cutting applications.
- Hub-type cutters are used for cutting internal gears.
- Rack-type cutters are ideal for cutting straight-toothed gears.
The effectiveness of a gear shaper cutter directly influences production efficiency and the quality of the finished product. Poor-quality cutters can lead to frequent replacements, inconsistent gear profiles, and increased downtime due to maintenance issues.
The Impact of Downtime in Gear Manufacturing
Downtime in gear manufacturing refers to periods when production stops due to machine breakdowns, tool failures, or maintenance requirements. This can have several negative consequences, such as:
- Financial losses: idle machinery and workforce lead to significant operational costs.
- Production delays: missed deadlines and unfulfilled customer orders can harm a business’s reputation.
- Reduced efficiency: Repeated stops and starts can hinder workflow optimization.
By selecting the best gear shaper cutter, manufacturers can minimize these issues and maintain continuous production with fewer interruptions.
How the Best Gear Shaper Cutters Reduce Downtime
Investing in high-quality gear shaper cutters can lead to significant reductions in downtime through various mechanisms:
1. Optimized cutting speed
It is made for cutting speed, which is perhaps the largest driver of production time. Producers are also able to continue with their production without frequent interruption due to the breakdown of equipment. Wear resistance is one of the primary concerns of the finest gear shaper cutters to reduce halts in practical operation. As the working time of the tools increases, the replacement time is also minimized, hence cutting down the overall cost of maintenance. This durability helps to ensure that, for the industries relying on them, steady production is possible without disruption.
2. Improved chip removal
Another advantage of using the cutters is the fast removal of the chip, and this does not interrupt the processes. Effective removal of chips prevents the formation of blockages that may cause delays in operation. This feature ensures that the manufacturers do not have to intervene very often while completing the targeted production. There is also flexibility in the process of setting up; therefore, the amount of time taken in the process of calibration of the cutter is limited, and personnel are free to work. Because the tasks are scripted and flexible, therefore there is an easy transition from one task to the other, which makes it efficient.
3. Consistent quality
Rework is less necessary since it guarantees constant quality in every operation. Error risk is reduced by producing gears to precise specifications by precise cutting. Manufacturers can save time fixing flaws when fewer gears are rejected. This uniformity upholds high standards of quality while increasing productivity.
4. Boosting productivity
Industries that need to produce precision gears need a gear-cutting tool. By producing precise and effective outcomes, using the proper instrument minimizes downtime. Errors are reduced via precision cutting, which removes the need for laborious adjustments. This improved precision guarantees the uninterrupted operation of production processes. These instruments enable producers to achieve deadlines without sacrificing quality because of their increased cutting efficiency.
5. Longer tool life
Another aspect of quality gear-cutting tools is durability, as this makes the work go on without regular intermissions. They are developed from strong materials so that they do not degrade after many years of utilization. Reduced frequency of breakages and wear leads to less frequency of tool replacement, hence reducing maintenance costs. This reliability will go a long way in explaining the consistency that characterizes the production of gears. However, the most important factor in ensuring that the operations are running effectively is consistency.
6. Quick and Easy Maintenance
Modern gear shaper cutters are engineered for ease of maintenance. Features such as replaceable cutting edges or indexable inserts allow for swift maintenance procedures. For example, indexable gear shaper cutters utilize replaceable carbide inserts that can be easily swapped when worn out, ensuring continuous high performance without the need for frequent maintenance.
7. Advanced Coatings and Treatments
The application of advanced coatings, such as titanium nitride (TiN), on gear shaper cutters enhances their hardness and resistance to wear. These treatments reduce friction during the cutting process, leading to lower heat generation and extended tool life. As a result, the intervals between necessary maintenance are lengthened, contributing to reduced downtime.
Factors to Consider When Choosing a Gear Shaper Cutter
Choosing the right gear shaper cutter is crucial for minimizing downtime. Important factors to consider include:
- Material Compatibility: Ensure the cutter material is suitable for the gear material being processed. Using incompatible materials can lead to rapid wear and increased tool changes.
- Cutter Design and Geometry: Select the appropriate cutter design based on the gear type and production requirements. Optimal geometry ensures precise and efficient cutting.
- Coating and Surface Treatment: Advanced coatings can extend tool life and enhance performance, reducing maintenance-related downtime.
- Manufacturer Support and Service: Choose reputable manufacturers that offer after-sales support, spare parts availability, and technical assistance.
Maintenance Best Practices to Minimize Downtime
Implementing effective maintenance strategies is crucial for minimizing downtime associated with gear shaper cutters.
- Regular Inspection: Conduct routine inspections to identify signs of wear or damage early, allowing for timely interventions before significant issues arise.
- Proper Lubrication: Ensure that all moving parts are adequately lubricated to reduce friction and prevent premature wear.
- Adherence to Manufacturer Guidelines: Follow the manufacturer’s recommendations regarding operating parameters and maintenance procedures to ensure optimal cutter performance and longevity.
- Training and skill development: Invest in training for machine operators to ensure they are skilled in proper cutter handling and maintenance practices, thereby reducing the risk of operator-induced downtime.
Conclusion About How can the best gear shaper cutter reduce downtime?
Choosing the best gear shaper cutter is a strategic investment that directly impacts production efficiency and profitability. By opting for high-quality cutters with advanced features, manufacturers can achieve:
- Reduced maintenance and replacement costs
- Improved production consistency and quality
- Significant reductions in downtime
Implementing best practices and staying updated with technological advancements will ensure long-term success in gear manufacturing.
FAQs About How can the best gear shaper cutter reduce downtime?
In this article, I’ve provided detailed insights into how the best gear shaper cutter can help reduce downtime by enhancing precision and efficiency in gear manufacturing. If you have any additional questions or need more information, feel free to reach out to me directly—I’ll be happy to assist!
What are the benefits of gear shaper cutters?
These tools are helpful in the manufacturing of timing pulleys, sprockets, internal and external gears, and sprockets. They are manufactured in line with international standards and standard designs. Any machine can use the components that are produced in this way. Custom cutters are made using profile modification software.
What is the process of gear shaping in a pinion cutter?
Spur gears are produced using a commonly used method called gear shaping. During the traditional gear shaping process, the pinion cutter and the gear workpiece typically revolve equally with a specified gear ratio, which might result in a significant variance in the cutting area per stroke in cutting tooth gaps.
Which of the following is the fastest method of cutting gears?
The quickest way to machine gears is by broaching, done with a multi-toothed cutting tool called a broach. In general, every tooth on the broach is higher than the one before it. Consequently, as the broaching process advances, the depth of the cut deepens with each tooth.
How does a gear shaper machine work?
A gear shaper machine cuts gear teeth by using a reciprocating cutter that moves up and down while the gear blank rotates in sync. The cutter removes material to shape each tooth, with the machine indexing the blank after each pass until all teeth are formed.
You May Also Like
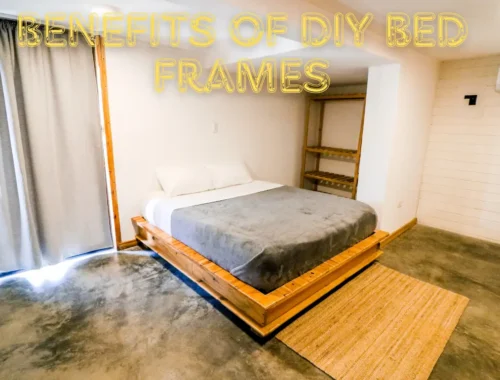
Benefits of DIY Bed Frames
29 May 2024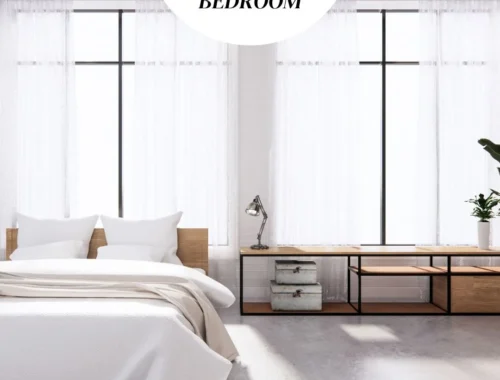
Mens Bedroom Ideas On A Budget
23 March 2024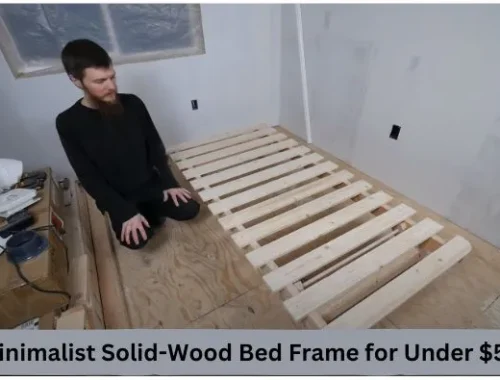