Meeting ISO 45001 Requirements for Workplace Safety
Table of Contents
ToggleStep-by-Step Guide to Meeting ISO 45001 Requirements for Workplace Safety
Ensuring a safe and healthy work environment is more than just adhering to the law, it is about safeguarding your employees. Organizations can manage safety hazards and create a strong safety culture by adhering to the ISO 45001 standard. To start, an ISO 45001 Course can provide a solid understanding of the standard’s principles and practices, helping you learn how to implement them effectively. Obtaining ISO 45001 certification entails elevating safety above and beyond the call of duty for all personnel including front line employees and upper management.
This blog will walk you through every step required to comply with ISO 45001 Requirements, simplifying how to maintain a safe and legal workplace while promoting an environment that prioritizes the safety of all employees.
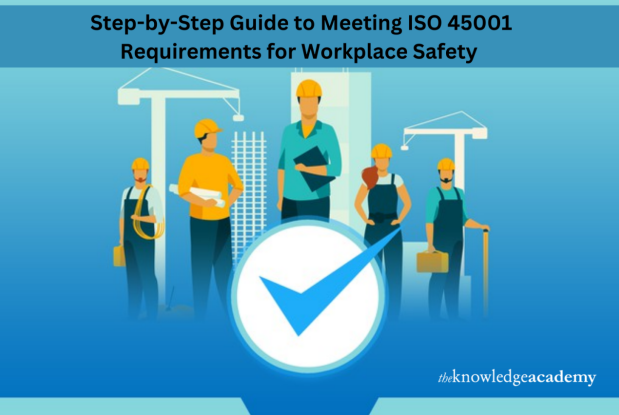
Step 1: Understand the ISO 45001 Standard
It is imperative to have a comprehensive understanding of the structure, guiding principles, and requirements of ISO 45001 before implementing it. Based on the Plan Do Check Act [PDCA] cycle, ISO 45001 emphasizes employee participation, continuous improvement, and risk management. Learn about the fundamental components of ISO 45001 such as:
- Context of the organization
- Leadership and worker participation
- Planning
- Supporting
- Planning
- Support
- Performance evaluation
- Improvement
To obtain ISO 45001 certification, specific standards must be fulfilled for each component.
Step 2: Conduct a Gap Analysis
A gap analysis is an essential step to find out how your present Occupational Health and Safety [OH&S] management system compares to ISO 45001 criteria. Identifying areas that require improvement entails thoroughly examining your current safety rules, procedures, and practices. Essential topics to concentrate on when doing the gap analysis are:
- Current risk assessment procedures
- Emergency preparedness plans
- Training and competency programmes
- Systems for observation and measuring
The analysis’s conclusion will offer a schedule for the required adjustments and assist in setting priorities for compliance related tasks.
Step 3: Secure Leadership Commitment and Involvement
To successfully implement ISO 45001, top management commitment is essential. The leadership group must proactively create the OH&S policy, establish goals, and allocate the resources required to ensure compliance. The leadership position ought to:
- Create and distribute an understandable OH&S policy that is in line with ISO 45001
- Set quantifiable goals and benchmarks for safety performance.
- Make sure that every level of the organization is actively participating.
- Provide enough funding to implement and maintain the OH&S management system.
An organizational culture of safety is fostered and established by management’s overt commitment to safety.
Step 4: Engage and Train Employees
Part of ISO 45001 is really about employee participation. Involving employees in planning and executing projects promotes a feeling of responsibility and provides insightful information about possible risks and hazards. Among the actions to guarantee successful worker participation are:
- Holding education seminars about ISO 45001 and its advantages
- Employee participation in risk assessments and decision-making
- delivering frequent instruction in emergency response, hazard identification, and safety procedures
- establishing avenues of communication for employees to raise risks and make suggestions for enhancements
Continual training is necessary to keep team members up to date on safety procedures and emerging hazards.
Step 5: Develop and Implement an OH&S Management System
Using the gap assessment results and the employees feedback, implement the OH&S management system that complies with the requirements of ISO 45001. The system should include:
- OH&S Policy: This crucial document serves as a tangible commitment from the Organization to the health and safety of all individuals involved, providing reassurance to employees and others affected.
- Risk Assessment: A systematic way of approaching risks to analyze them, evaluate them, and then put in place the necessary measures to mitigate them.
- Legal Compliance: These measures are crucial for ensuring the Organization meets all health and safety legal requirements and standards, thereby promoting a safe work environment.
- Emergency Preparedness: A specific or detailed arrangement regarding aspects such as fire alarms, chemical spills, and other related emergencies or perhaps a health complication.
- Operational Controls: Activities in an organization to address the risks and hazards known to a company in its day-to-day operations.
Ensure all the guidelines are recorded somewhere, let employees know about them and make them available.
Step 6: Monitor, Measure, and Evaluate Performance
Continuous improvement requires measuring and monitoring OH&S performance. Create a system for evaluating performance that consists of:
- Routine internal audits to assess adherence to ISO 45001 standards
- Tracking of safety-related key performance indicators [KPI] such as incident, near-miss, and training completion rates
- Carrying out management reviews to determine opportunities for improvement and assess how well the OH&S management system is working
Action plans for correcting non-conformities and improving safety performance are created using the information gathered from audits and reviews.
Step 7: Conduct Internal Audits and Management Reviews
Internal audits are crucial to ensure that the OH&S management system operates as planned and fulfils ISO 45001 criteria. To offer an unbiased evaluation, internal auditors must possess independence and training. The following are involved in the internal audit process:
- Creating a checklist and audit plan by ISO 45001 standards, carrying out the audit, and gathering data via observations, interviews, and document reviews
- Presenting results and suggesting areas for development
Management reviews should be carried out after internal audits to evaluate the OH&S management system’s overall efficacy. The following should be the main topics of these reviews:
- Results of internal audits and evaluations
- Achievement of safety objectives and targets
- Changes in internal and external factors affecting the organization
- Recommendations for improvement
Step 8: Continual Improvement and Corrective Actions
Continuous improvement is emphasized by ISO 45001 as a fundamental principle. Organization’s should set up procedures for locating, recording, and implementing remedial actions to resolve non-conformities and stop them from happening again. This includes:
- Examining the underlying causes of accidents, close calls, and audit results
- Creating remedial action plans with defined roles and due dates
- Evaluating the results of actions taken and making necessary modifications
Promote a mindset that values making amends for errors and utilizing criticism to propel continuous advancements in worker safety.
Step 9: Prepare for Certification
It is time to prepare for the certification audit after the OH&S management system is fully operational and the business is specific, following ISO 45001 requirements. This includes:
- Deciding on an established certification authority authorized to carry out ISO 45001 audits
- Evaluating certification to find any outstanding gaps
- Supplying the certification body with the necessary records and proof of compliance
- Resolving any issues or inconsistencies found throughout the audit for certification
A successful certification process indicates an organization’s dedication to upholding a secure and healthy work environment.
Conclusion
The systematic process of implementing ISO 45001 calls for thorough preparation, cooperation, and dedication from all organisational levels. By following this step-by-step guidance, organizations may create a strong OH&S management system that satisfies ISO 45001 regulations and fosters a continuous improvement and safety culture. Obtaining ISO 45001 certification, with the proper training and support from providers like The Knowledge Academy, can increase business performance in general, lower workplace incidents, and boost employee morale.
Common FAQs
1. How to implement ISO 45001 in the workplace?
Identify hazards, assess risks, set safety policies, involve employees, and continually improve safety practices.
2. What is the safety management system as per ISO 45001?
A framework to manage workplace safety through risk control, policies, and employee involvement.
3. What is the ISO for work safety?
ISO 45001:2018, the global standard for workplace health and safety management.
4. What are ISO 45001 requirements?
Leadership, employee participation, risk assessment, hazard control, and continual improvement.

Etsiosapp release date
You May Also Like
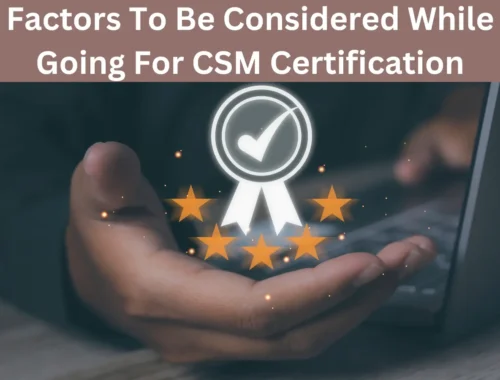
Factors To Be Considered While Going For CSM Certification
10 January 2025
Boost Your CLBPT Score: Comprehensive Practice Tests and Strategies
25 November 2024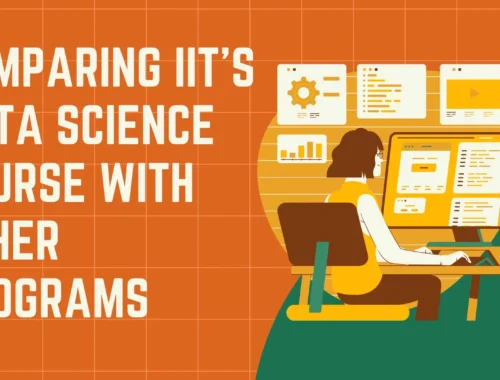